- Codman Cmc Irrigation Service Manual Pdf
- Codman Cmc Irrigation Service Manuals
- Codman Cmc Irrigation Service Manual Instructions
- Codman Cmc Irrigation Service Manual Diagram
Manuals, IFUs, recalls & alerts incl Malis Advantage Maintenance Manual Rev A, MALIS Bipolar ESU CMC-III Service Manual Aug 1998, The MALIS CMC-III Bipolar Electrosurgical System Instruction Manual Revised Oct 2010, MALIS MODULE 1000 Irrigation System Instruction Manual Revised May 2012, MALIS CMC V Quick Start Guide ELS-38-000 Aug 2011, and Malis Advantage Maintenance Manual rev A&hellip. Specifications: Malis Codman CMC II Coagulation Unit 80-1160 Serial# PC1268 Malis Codman CMC II Irrigation Unit 80-1164 Serial# IR2549 Polymount Rolling Stand Footswitch Connection Cables 110-115 VAC 50/60 Hz Made IN USA International buyers contact me for a shipping quote to your country.
Internationally Trusted & Used
- Read Book Codman Malis Cmc Iii Service Manual Codman Malis Cmc Iii Service Manual Overdrive is the cleanest, fastest, and most legal way to access millions of ebooks—not just ones in the public domain, but even recently released mainstream titles. There is one hitch though: you’ll need a valid and active public library card.
- Product Code Name & Description 80-1788 ®CODMAN MALIS ® CMC V GENERATOR (English) includes: ® CMC V Bipolar Electrosurgical Generator unit, ®CMC V Foot pedal and power cord. 80-1569 ®CODMAN MALIS ® CMC V MODULE 1000™ IRRIGATOR includes: CMC® V MODULE 1000™ Irrigator ®CMC V Interconnecting Cable and standard power cord.
- Mazda mpv v6 1998 repair manual codman cmc service manual mklll diesel codman service manual tricia joy manual codman malis cmc v service manual documents 2004 suzuki vinson 4x4 manual service manual codman cmc priority downloads trac workshop codman malis cmc v service manual tricia joy kenmore elite ultra wash browse codman cmc manual.
Contact our UK representative
The Clinical Equipment Library and the Surgical Equipment Library, with one-click switching between them. Key features:
One-Click Access from your hospital intranet
Product Recalls and Alerts
Skills Checklists
Pocket Reference Guides
Cleaning & Sterilisation Instructions
User Guides
Instructions for Use
Addendums
Codman Cmc Irrigation Service Manual Pdf
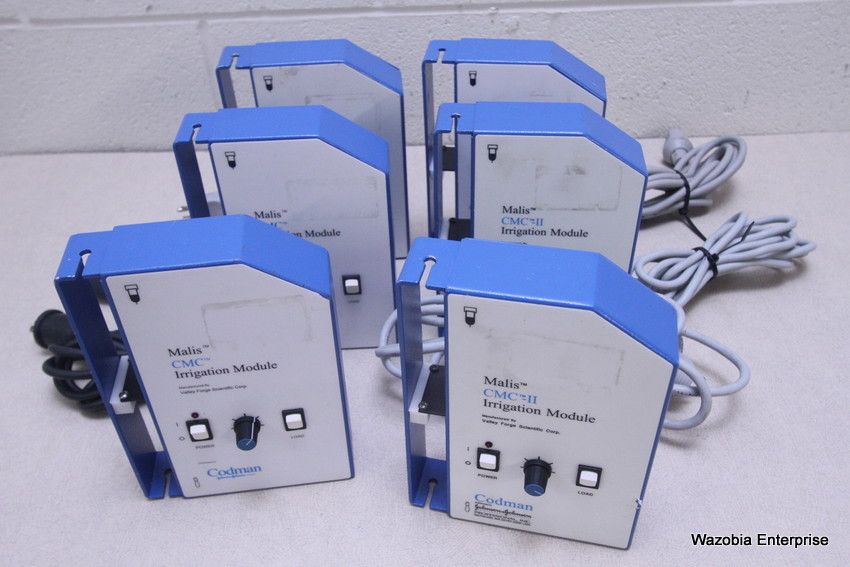
Procedure Guides
In-Service Videos
Codman Cmc Irrigation Service Manuals
Don't miss the December 2020 deadline! BioClinical Services to the rescue!
Rate Action 3.14 as satisfactorily met only if a health service organisation demonstrates progress towards full implementation as set out in their implementation plan for AS/NZS 4187:2014
Codman Cmc Irrigation Service Manual Instructions
5.4 Documentation
A prime responsibility of the administration of a health care facilityis to ensure that proper and adequate documentation systems are established and observed. Such systems should include (but not necessarily be limited to the following:c) Supply and availability of equipment documentation, including operating instructions, service records, fault reports, hazard tags.5.5.3 Operator instructions
Most equipment requires some operator proficiency. Formal instruction of staff in operation of equipment should be performed, particularly when new staff or new equipment is concerned. User manuals, written in English and in terms acceptable to the user, should be available to the user at all times, near the equipment. Colour illustrations should not be relied upon as the sole means of identifying or clarifying important instructions or warnings.MHRA Managing Medical Devices April 2015 Guidance for healthcare and social services organisations
7.1 Instructions for Use
Clear responsibilities should exist for ensuring that the manufacturer’s instructions are passed on to all usersCQC Care Quality Commission Regulation 15: Premises and equipment
Codman Cmc Irrigation Service Manual Diagram

We offer discounts for 3 year contracts and groups of hospitals, even further discounts for small hospitals. Contact us for current pricing.
Save 10% on individual libraries on a 3 year contract
Save 25% on both libraries on a 3 year contract if each hospital has>100 beds
Save 35% on both libraries on a 3 year contract if each hospital has<100 beds
Chat to us instantly online right now, call or email our core team directly. Get in touch about anything and everything.

George Koning
Chief Executive Officer
Therese Koning
National Sales Manager
Adam Hill
Chief Technology Officer
~~ PRO FESSI O N A L, INC. RAYNHAM , MA 02767-0350 USA ~ if • ..........'o/ Lecnln;ll. Malis. IolD. · CMC is I regisll<ed noarnarlt 01 JoMscn & .JotrsorI Proleucn:l~ II'IC.
3.0 Service and Repair .................................... IFe 4.0 Warnings and Cautions ............................. IFe
improper service. THE ABOVE WARRANTIES ARE IN LIEU OF ALL OTHER WARRANTIES, EITHER EXPRESS OR IMPLIED, INCLUDING ANY WAR· RANTY OF MERCHANTABILITY OR FITNESS FOR A PARTICULAR PURPOSE. Suitability for use of the device for any surgical procedure shall be determined by the user. Codman shall not be liable for incidental or conseque~tiaJ damages of any kind.
5.0 Functional Description of Controls and Indicators ................ ..... _. 1
3.0 SERVICE AND REPAIR
TABLE OF CONTENTS ' .0 Scope ......................... ...... ......................... IFe 2.0 Warranty ............................... .................... IFe
5.1 Product Description ................................ 1 5.2 Generator Controls ................................. 1 5.3 Remote Control Set Controls .................. 2 5.4 Footpedal Controls .................... __ ....... .... 2 5.5 Indicators ................................ ......... _... _.. 3 5.6 Connections ............................................ 4 6.0 Technical Description .................................... 4 6.1 Printed Circuit Boards ............................ 4 6.2 Theory of Operation ................................ 5 6.3 Master List of Card Connector Signals ..........................••.... 10 6.4 Test Points ............................................ 11 6.5 Operational Performance ...................... 12 6.6 Calibration ..... ....................................... 12 6.7 Technical Specifications ....................... 13 6.8 Trouble Shooting Guide ........................ 14 7.0 Replacing Internal Fuses ............................ 14 8.0 Maintenance ............................................... 15 9.0 Routine Cleaning ......•...................... ........... 15 10.0 Sterilization ............................................... 15 11 .0 Block Diagrams ......................................... 16 12.0 Schematics ............................................... 20 13.0 PCB Layouts and Assemblies ................... 34 14.0 Parts List ................................................... 46
1.0 SCOPE This manual contains the necessary information to allow a qualified Service Technician to perform maintenance and repair in the field. If the unit is still under warranty, please refer to Section 2.0.
For service or repairs to the MALIS CMS-III generator and footpedal, contact your local Cadman sales representative directly or through Cadman Customer Service , 1-800-225-0460. The sales representative coordinates the return to: Codman Repair Service c/o Johnson & Johnson Professional, Inc.
4969 Wakefield Street Philadelphia, PA 19144
Include with the unit a repair purchase order number,
the serial number of the generator, and a written description of the problem. The MAllS CMG-rrr Remote Control is not repairable. Replacements are available from: Johnson & Johnson Professional, Inc. 325 Paramount Drive Raynham, MA 02767-0350
4.0 WARNINGS AND CAUTIONS 4.1 WARNINGS 00 not attempt to bypass the grounding prong on the generator by using a 3-prong to 2-prong adaptor. The generator must be properly grounded to ensure operator and patient safety. Grounding reliability can be achieved only when connected to a receJr tacle marked 'Hospital Only' or ' Hospital Grade'. Always replace the system's fuse with the appropriate type and value fuse (see Technical Specifications). The unit should not be modified in any way by any user. Unauthorized modifications to the unit may cause it to malfunction or fail in use.
2.0 WARRANTY
4.2 CAUTIONS
The MALIS Bipolar Electrosurgical System CMC-III (catalog no. 80-1170) is warranted for one full year from date of purchase, except the Remote Control Set which is warranted for six months. The MALIS CMC-1I1 is warranted to be free from defects in both materials and workmanship. This warranty shall not apply where service is required due to (i) Buyer's failure to operate or maintain the Equipment according to the Instruction Manual, (ii) Buyer's use of unauthorized parts or consumables, (iii) accident, abuse, misuse, modification or misapplication, or (iv)
Continuous power output, by either footpedal or remote control, must be limited to 20 seconds, with a 4O-second rest period . Close proximity of this unit and its cables with some Electrosurgical Units producing EXCESSIVE RF CURRENT RADIATION may cause this unit to produce voice annunciation and possibly output power. We recommend the user insure MAXIMUM PHYSI· CAL SEPARATION of this unit from any other electrosurgical device and its cables.
5.0 FUNCTIONAL DESCRIPTION OF CONTROLS AND INDICATORS 5.1 PRODUCT DESCRIPTION The MAUS Bipolar Electrosurgical System CMC-III (catalog no. 8()'1170) includes: 1. The Generator; 2. A wireless Remote Control for changing power settings as well as operating the cutting and coagulation functions;
3. An Adapter Cable to allow the use of a MALIS Irrigator and/or a MALIS Bipedal Electric Footswitch with the CMC-IJI . The generator is compatible with both a pneumatic footswitch (catalog no. 8(H173) and an electric tootswitch (catalog no. 80-1149) both available
separately. The generator is equipped with a voice synthesizer that provides an audible indication of changes to the power settings. At the surgeon's option, it also announces the operating mode and power setting each time cutting or coagulation is
performed. With the exception of the generator, aU the above system components may also be ordered
5.2 GENERATOR CONTROLS (Figures 1 and 2) A. Power Switch Controls the power supplied to the coagulator.
B. Cutting Power Control Switch Used to increase or decrease the power settings for cutting . (Cutting power control buttons are also located on the remote control set.) C. Coagulation Power Control Switch Increases and decreases the power settings for coagulation. (Coagulation power control buttons are also found on the remote control set.) D. Tone Volume Control Used to control the volume of the tones which indicate cutting or coagulation power is being delivered to forceps. You can change the tone volume at any time during the operation of the CMC-III , except while cutting or coagulating. While you are using these controls, the tone volume settings appear in the Microcut Power Display Window (Item V in Figure 5). Afterwards, the display window again shows the actual microcut power setting .
separately. MAUS Bipolar Cutting Forceps and standard insulated and non insulated forceps are available separately, as are reusable and disposable bipolar cords. The System may be used with the MALIS Irrigation Module (catalog no. 80-1164). The CODMAW Floorstand for MALIS CMC-IIIIII is designed to accommodate the CMC-III Generator and the Irrigator together. In bipolar coagulation, the electrical difference is onty in the isolated output and in the lower power requirements. The output of the bipolar generator should be isolated from ground as much as possible. so all current flow takes place between the two tips of the separated forceps. There should be virtually no current flow from either side of the forceps to ground. The current geometry will now be dependent upon the tip size and the angle at which the tips meet, as well as the medium in which they are immersed. 11 the forceps blades are virtualty parallel. and the forceps are deep in saline, there will be major shunting in the saline. If the forceps are bowed or angled so the tips almost meet while the blades are still well separated , the current flow will be mainly between the tips with little shunting. The lowest possible generator output impedance provides the best maintenance 01 power at the forceps tips with the least decrease in coagulation due to shunting. The MAUS Bipolar Electrosurgical System CMC-III provides the higher energy output needed for rapid cutting of all tissues, including dense fibrous layers, shifting the low impedance of the micro cutting automatically to match the power requirements of the high power cut settings.
----.
B
C
CHe ·1lI
]~
0
-
0
0
-.. 0
A
'
0
I
0
0
I
I ©.::[email protected]
D
E
Figure 1. Front Panel Controls (Items A through I)
E. Voice Volume Control Used to increase or decrease the volume of the voice synthesizer which announces the operating mode being employed and changes in the power settings. You can increase or decrease the voice volume at any time while using the CMC-III, except during cutting or coagulating. While you are using these controls. the voice volume settings appear in the Microcut Power Display Window (Item V in Figure 5). Afterwards, the display window again shows the actual microcut power setting.
F. Cutting Reset Button By pushing this button , you can immediately reset the cutting power to 35 Malis Units (or 9 watts).
1
G. Coagulation Reset Button You can quickly reset the coagulation power to 35 Malis Units (or 9 watts) by pushing this button.
H. Irrigation Mode Sutton When the MAUS Irrigator is properly set up and connected to the CMC-III, push this button to disable and enable irrigation. An additional irrigator button is located on the remote control set. The Irrigation Mode Indicator (Figure 5, Item AA) located on the generator will illuminate when the irrigator is enabled , regardless of which of the two switches is used .
I. Watts Display Button Press this button to display the power settings in watts. The Watts Display Indicator (Figure 5, Item CC) illuminates whenever power settings show in watts.
J. Voice Mute Button Used to prevent the voice synthesizer from announcing the operating mode being employed and the power settings each time cutting or coagulating is performed. When the voice is muted, the Mute Indicator, Item BS in Figure 5. illuminates. K. LED Test Button When you press this button , all numeric LEOs should illuminate as a self-diagnostic test. Any numeric LED that does not illuminate , Signals a problem requiring attention .
N. Coagulation Output Button By pressing this button. you cause coagulation power to be delivered to the forceps. (The Coag pedal on the footpedal, Item S in Figure 4, also controls this function .)
O. Coagulation Power Control Button Use this button to increas~ or decrease the power setting for coagulation . (The Coag Power Control Switch on the generator, Item C in Figure 1, controls the same function .) P. Cutting Power Control Button Increase or decrease the power setting for cutting by means of this button. (The Cutting Power Control Switch on the generator, Item B in Figure 1, controls the same function .) Q. lrrlgatlon Mode Button When the MAUS Irrigator is property set up and connected to the CMC-III , push this button to disable and enable irrigation. An additional irrigator button is located on the generator. The Irrigation Mode Indicator (Figure 5, Item AA) located on the generator illuminates when the irrigator is enabled. regardless of which of the two switches is used.
-- _-.,' =
~
-
L. Supply Voltage Selector Use this control to set the generator to the same voltage as the power receptacle you are using.
N
a
Mali,-
=
<>
K J I
p
LJ
LJ
Figure 2. Bad< Panel Controls (Items J through L)
5.3 REMOTE CONTROL SET CONTROLS (Figure 3) M. Cutting Output Button When you press this button, cutting power is delivered to the forceps. (The Cut pedal on the footpedal. Item R in Figure 4 , also controls this function.)
'',& ~
~
o
FIgUre 3. Remote Control ptems M through Q)
5.4 FOOTPEDAL CONTROLS (Figure 4) R. Cutting Output Pedal When you depress this pedal. cutting power is delivered to the forceps. (The Cut button on the remote control, Item M as shown in Figure 3, also controls this function .)
lor is initially turned on, the setting -35- will appear in both the microcutting and coagulatkm windows. The high power cutting window will be blank. The following power settings are available for each operating mode.
COAG
CUT
POWER SEmNGS COAGULATE
MICAOCUTTING
HIGHPOWEA ClfTilNG
Malis Units Watts
Malis Lklits Watts
MarIS Units Watts
•
10 15 20 25 30 35 40 45
R
$
Figure 4 . Pneumatic FootpedaJ Controls (Items R and S)
S. Coagulation Output Podol Coagulation power is delivered to the forceps when you depress this pedal. [The Coag button on the remote control, Item N as shown in Figure 3, also controls this function.)
NOTE: Cutting and coagulating power may also be controlled using the MALIS Bipedal Electric Footswitch (catalog no. So-' 49) connected to the CMC·JIJ via the Adapter Cable (catalog no. 80-1179). Refertothe adapter cable instructions for details.
~~
O!C' I11
-. U :~
~-.
§
D:;LJ DO
11 .0 14.0 17.0 19.0
I .•
30 35
3.0 5.0 7.0 9.0
50
11.0 14.0 17.0
2$
..'
60 70 80 90 100 110 120 130
''
150
20.0 '.0 60.0 80.0 100.0 120.0 140.0 160.0 180.0 200.0
22.0 24.0 25.0
29.0 32.0 35.0 '.0 45.0 SO.O
X. High Power Cutting LED This yellow LED illuminates whenever cutting power in the high range (60 to 150 MALIS units, or 20 to 200 watts) is delivered to the forceps. This yellow LED illuminates when cutting power in the micro range (8 to 50 MALIS Units , or 0.7 to 17 watts) is delivered to the forceps.
V, i= v w z
........ . --
I .•
3.0 5 .0 7.0 9.0
•
10 15 20
0.7 1.0
Y. Mlcroeuttlng Power LED
5.5 INDICATORS x u
SO 60 70 80 90 100 110 120 130 140 150
0 .7 1.0
-
AA 0 _
-
0_
[;IEiIEiI ; I I ~~ 1
BB
cc T
LJ
FJgl(re S. Front Panellndicator.i (Items Tthrough DO)
T. Power Output LED This green LED illuminates whenever power of any kind, for either cutting or coagulation, is delivered to the forceps.
U-W. Power Display Windows These three sets of windows show the power selections for high power cutting (Item U) I microcutting (Item V). and coagulation (Item W) . The power selections can be shown in either MALIS Units, or watts; use the Watts Display Button (Item I in Figure 1) to make your choice. When the genera-
Z. Coagulation Power Light This blue light illuminates whenever coagulation power is delivered to the forceps. AA. Irrigation Mode LED Irrigation is enabled when this green light is on and a MAUS Irrigator is property connected. NOTE: To avoid unintentional irrigation , be sure the power on the Irrigator is switched off whenever the CMC-III generator is switched off.
BB. Mute LED When you disable the voice synthesizer by using the voice mute button (Item J in Figure 2), this green LED lights up. CC. Watts Display Indicator If you choose watts to be displayed in the power indicator windows (Items U, V , and W. Figure 5) by pressing the watts display button (Item I. Figure 1) , this green LEO illuminates. DO. Infrared Signal Receiver Window This window receives signals from the remote control set. Do not obscure the window during use.
3
Tone Indicators (not shown)
The CMc..1II generator produces a tone whenever power is delivered to the forceps. Two different tones are employed to differentiate between coagulation and cutting. A low frequency major chord indicates coagulation. A higher frequency minor chord indicates cutting. You can control the volume of the tone indicator with the tone volume control (Item 0 in Figure 10).
Voice Indicator (not shown) The voice indicator enables you to check or adjust the power setting and mode of operation without removing your eyes from the surgical site. As you change the power setting. the voice indicator announces each new setting. When you use the Cut switch (on either the remote control set or the footpeda/) the voice announces either 'Microcut' or 'Cutting·. It also announces the power setting before the generator delivers either cutting or coagulating power to the forceps. You can use the voice volume control (Item E in Figure 1) to change the volume 01 the voice. In addition, the voice indicator functions as part of the setf·diagnostic feature for the five conditions shown below.
FF. Pneumatic Footpedal Receptacle Accepts the connector of the pneumatic footpeda!.
GG. Irrigator Receptacle You may plug the CMC·III Adapter Cable (catalog no. 80-1179) into the generator here to use the MALIS Irrigation Module (catalog no. 80-1164) and/or the MAliS Bipedal Electric Foptswitch (catalog no. 801149) along with the CMC·111. Refer to the set up instructions in the manual supplied with the adapter cable for more information.
NOTE: To avoid unintentional irrigation, be sure the power on the Irrigation Module is switched to the OFF position whenever the power switch on the CMC·III generator is in the OFF position. HH. Power Receptacle This receptacle accepts the three-prong power cord plug and also contains the supply voltage selector and external fuses. (See Technical Specifications.)
II. Equipotential Connector Use this terminal to connect a potential equalization conductor to a busbar in rooms where potential equalizabon is required.
c:
'Memory Error'
't::::::l
~ -~
-
AL
~-.~ .. :ii:i: ...
Operating maffunction
, ':::;
Indicates the two front panel power setting controls were pressed simuttaneousty
11011 ~!= -:'.':.
LJ
'
LJ
HH
Figure 7. Back Panel Corlnedion$ (Items FF through II)
Refer to the Section 6.8, Troubleshooting Guide, for further information.
6.0 TECHNICAL DESCRIPTION
EE. lsolated Bipolar Output Jacks These jacks accept the banana·type plugs of either the reusable or disp0sa.b4e bipotar cords.
---
~
OC·1lI
[email protected] I.ffill
• I ~ I ~.
L,-------''-'=-..''F'ir'-J- EE LJ
F'9ure 6. Front Panel Connections (Item EE)
U
GG
Fi~
'Internal Power Error' Operating malfunction
5.6 CONNECTIONS (Figures 6 and 7)
FF
liE·f',
Indicates that both footpedals were pressed simultaneousty
4
_ _· 0 0
11'11
Indicates an internal fuse must be replaced
6.1 PRINTED CIRCUIT BOARDS (PCBs) 6.1.1
Mother Board The Mother Board consists of low voltage power supplies, an infrared remote control receiver. open circuit detector, pneumatic footswitches, tone, and voice volume control switches. RF output DC blocking capacitors, and all cardedge connectors necessary for joining the printed circuit boards.
6.12
Display Board
The Display Board consists of numeric Ught Emitting Diode (LED) displays, single LEOs, pushbutton, and rocker·type switches.
6.1.3 Controller Soard The Controiler Board houses an B-M RCNHARRIS 1805 microprocessor (JtP). Also included are clocks, watchdog timer, clock synchronizer, and inpuVoutput (I/O) control (N.lines).
6.1.4 Sound Board The Sound Board consists of a Digitaiker™, EPROM , digital tone generators, steering logic, audio fitters, amplifiers, and two electronic volume controls for voice and tones.
6 .2.1.6
Open Circuit Detector
The Open Circuit Detector circuitry is located primarily on the Mother Board , with interfacing elements on the RF Power Amplifier Board.
6.1.5 High Voltage Power Supply Boord The High Voltage Power Supply Board is an off-line switching-type power supply utilizing the f1yback principle of voltage transfer and isolation from power line (mains) sources.
The open circuit detector helps prevent excessively high cutting voltage during periods of open forceps tips from breaking down components in the RF path. It also eliminates the occurrence of AF interference. This circuit is active only during the high power cut mode .
6.1.6 AF Power Amplifier Board The RF Amplifier Board consists of a bridge-type RF
Operation is as follows:
amplifier, coagulation waveform generator, RF output steering, short circuit detection, and isolated bias supplies.
6.2 THEORY OF OPERATION NOTE: Refer to each board's block diagram and schematic, Sections 8.0 and 9.0, respectively.
6.2.1 Mother Board 6.2.1.1 Low Voltage Power Supplies Four low voltages are supplied on the mother board :
(a) +5 VDC @ 2 Amps (regulated) ; (b) +15 [email protected] 1 Amp (regulated) ; (e) +18 VDC @ 1 Amp (unregulated); and, (d) ·18 [email protected] Amp (unregulated). 6.2.1.2
Infrared Remote Control Receiver
The Infrared Remote Control Receiver monitors aaivity from the infrared remote control handheld transmitter, and sends the serial data to the IlP for processing. 6.2.1.3
Pneumatic Footswitches
Air pressure from the cut and coag footpedals preSSUriZe their respective air switches. Signals are sent to the J.l.P for processing . 6.2.1.4
Tone and Voice Volume Control Switches
The Tone and Voice Volume Control Switches are located on the front of the Mother Board, protruding through the front panel of the CMC· 1I1. Signals from these switches are sent to the 'p for processing. 6.2.1.5
DC Blocking Capacitors
A capacitive DC block is inserted between the output of the RF Amplifier and the forceps to limit DC circulatory current that occurs during cutting or coagulating to prevent muscle tissue reaction.
A small ( <3 V p oP) audio signal of approximately 20 Khz is generated by U602 in the form 01 a sine wave, buffered by Q600 and capacitor coupled to transformer TS02 and C529. This is the 20KHZOUT signal. The primary of TS02 and capacitor C529 form a parallel resonant circuit. Signal 20KHZlN is a path to a filter, buffer U603B, detector, and threshold comparator U603A. Providing there is essentially an open across the secondary winding of TS02 (forceps open) , the parallel resonant circuit acts to impede the flow of the 20 Khz sine wave from 20KHZOUT to 20 KHZlN. During this period of open forceps, U603A toggles on and asserts the ?WRDIS signal to U503 on the RF Amplifier Board, thereby shutting off RF power If the forceps should see resistance under 5000 ohms, the secondary winding of T502 acts to reflect this impedance back to the primary winding of T502 and lower the Q of the parallel resonant circuit, thereby aflowing the 20 Khz sine wave to pass from 20 KHZOUT to 20 KHZIN. This signal level is detected by 0600 and 0601 , causing comparator U603A to change state and allow the RF amplifier to operate.
Time delay is built into the detector circuit to allow continuous application of RF power during short periods of open circuit. After approximately 0.5 seconds of open circuit at the forceps, RF power is extinguished . L504 and C530, on the RF Amplifier Board, is a series resonant circuit that acts to prevent the 1 Mhz RF power waveform from saturating T502 and interfering with the low level detection circuitry.
6.2.2 Display Board 6.2.2.1 Front Panel Numeric LEOs LED101 through LE01 08 are driven by U101 through U108, respectively. Data from the 808ft Oata Bus (D8{O .. 1}) are la1ehed into Ul0l·Ul08 from control signals supplied by Ul09, Ul10, and Ulll . The latched information is decoded (hexadecimal to 7 segments) and drives the numeric LED displays.
5
Steering klgic, consisting of Ul09 through Ull1, suppty control signals to U101 through U1 08. The N1 signal selects the most significant byte of the Cut and Coag displays, the decimal points used on the Microcut and Coag displays, as well as the two least significant bytes on the Cut, Microcut, and Coag displays. The N1. N2. HPCUT. LPCUT. and COAG signals combine, respectively, to select the proper numeric LED display. The HPCUT. LPCUT. COAG . BLINK. and FTPOON signals combine to flash the selected numeric LED display when RF power output is requested . 6.2 .2.2
Front Panel Single LEOs
The HPCUT. LPCUT. COAG . and FTPDON. signals are combined, selectively, to tum on the HPCUT, LPCUT. or COAG mode display LED~amp . The FTPoON signal turns on the Generator LED when RF output power is requested. The MUTELEo signal turns on the Mute LED when voice muting is requested. The IRGLEo signal turns on the Irrigate LED when irrigation is requested. The WATTS LED signal turns on the Watts LEO when the watts display mode is requested . 6.2.2.3
Front Panel Switches
The UP/DN signal is produced by the RF power control rocker switches, 5101 and 5102. The CUTSTRB signal is produced by the Cut RF power control switch, 5101 . The COAGSTRB signal is produced by the Coag RF pO¥ler control switch , 5102. The IRIGSW signal is produced by the Irrigator control switch, 5103. The WATISW signal is produced by the watts switch , SlO4. The CUTRST signal is produced by the Cut Reset switch . S105. The COAGRSTsignai is produced by the Coag Reset switch, 5106. 6 .2.2.4 LPop
On-Card Signals High going signal indicating seled.ion of the microcut decimal point
CGop High going signal indicating seledion of the coag decimal point
6.2.3 6.2.3.1
Controller Board Microprocessor
The microprocessor has an a·bit bidirectional data bus (OB{O.. 7}), 16-bit memory addressing (641<) and appropriate timing indicators (TPA, lPB, MRD. MRW) , a device 1/0 selection (N. lines) , 4 extemal flag-line inputs (EF1 to EF4) , extemal interrupt (INTIJ , internal countdown timer, and 64-byte random access memory (RAM). An N-line decoder, U205, provides one-ot-eight operation of I/O devices (N1 to N7) .
6
6.2.3.2
Memory
The memory circu;t has fully demultiplexed 16-bit addressing to allow 64k-bytes of data. Memory consists of one 27128 EPROM (16k-bytes). one 2805 EEPROM (O.5k-bytes) and a fl4.byte RAM in the J.lP. Upper 8-M addressing (of 16 bits) occurs during the Timing Pulse A (TPA) period, and is latched tnto U207 and U208. U201D and U233C provide enabling/disabling signals to all the memory devices to avoid conflicting with one another. 6.2.3.3
Clock Generator
The clock generator includes a stable a Mhz crystal and two ripple dividers, U202 and U203. RipP'e dividing provides continual. phase coherent division from 4 Mhz to .25Hz in divide--by·two steps. Approximately eight taps are used by devices on the controller board. 6.2.3.4
Watchdog Timer
The watchdog timer, U206, provides a reset pulse to the J.lP when one of the following occurs: (a) power up; or, (b) no signal .to U206, pin 6, watchdog input (WDI) within 1 to 2.5 seconds, continuaJly. This guards against unit matfunctioning due to IJP hang·ups and temporary low supply voltage condi· tions. 6.2.3.5
Clock Synchronizer
The f,1P internal clock divider is synchronized with the external clock generator. A flip-flop, U231 B, whose output changes only with a rising clock edge on the clock input. is supplied with a 500 Khz clock. The 500 Khz clock is the equivalent of the intemal clock frequency of the J.lP. When the watchdog timer signals a ·clear' to both the synchro circuit the rising edges of both the 4 (U231B) and the Mhz and 500 Khz clocks are aligned and the IJ.P starts running synchronously with the master clock generator.
.p.
6.2.3.6
Select Out
Data to be output from the 8-bit data bus are latched into U212. U213. U214, and U215 when the NS, N6, MRo. and TPB signals are synchronous. 6.2.3.7
Select In
Data to be input to the 8-bit data bus are transmitted through U216. U217. U218. U219. U237. and U238 when the N3, N5. N6, and MWR signals are synchronous.
6.2.3.8
Digital-to-Analog Converter (CAC)
The OAe takes information from the S-bit data bus and converts it to analog voltage information used by the High Voltage Power Suppty. Eight bits of hexadecimal data corresponds to 256 units of decimal data, as is applied to the DAe. HEX data are loaded into the DAC when the N4 and MRD signals are synchronous. The value of the 4.75 vec reference output from the DAC will be (NJ256)' (4.75 VDC). wtth N=hexadecimal value input to CAe. 6.2.3.9
Randomizer Control
When the U229 divider ratio is changed and shifted by a 488 Hz clock, the output of the PLL VCO, U228, is 8 Mhz, ± 4% at a change rate of 488 Hz. Further division of the shifted 8 Mhz waveform is handled by the 1 Mhz Split-Phase Dead Zone Generator. The 8 Mhz shifter circuit is locked to one frequency near 8 Mhz during the cutting mode . 6.2.3.12 1 Mhz Split-Phase Dead Zone Generator
The AF Power Amplifier bridge field-effect-transistors (FETs) require a 1 Mhz signal . However, due to the tum off delay propagation nature of FETs, a somewhat shorter duty cyde (37% on, 63% off) is required to prevent both halves of the bridge from turning on at the same time and reducing efficiency. Eight Mhz from the 8 Mhz shifter circuit is sequentially divided by two through U230A, U230B, and U231A to 1 Mhz. The outputs of U230A and U230B are ANDed together through U2330 and delayed through U234A and U2348. They are combined (ORed) with the 1 Mhz and 1MhZ outputs of U231A through U232A and U232C to form two 37% duty cycle waveforms, 01Mhz and 01Mhz. The C1Mhz and 0 1Mhz rising edges are shifted 1SOO from each other for proper RF bridge amplffier operation .
While pseudorandomization data (necessary for coagulation) is primarily maintained by a data table in the EPROM and controlled by the ~p, U225 assists the ~P by providing delays not otherwise obtainable by the ~P itself. When N7 is asserted, data from the S-bit data bus are loaded into an 8-bit binary downcounter, U225. U225 is clocked down at 1 Mhz. Therefore, each data byte latched into the counter inputs represents a delay in one-microsecond increments (j.LS) (e.g.; hex 10=10 J.lS, hex 38=59 )lS). The delay is used to control the start of the coagulation waveform bursts. When U225 is finished downcounting a given data byte, it signals the ~P via the EFl flag line input.
6.2.3.13 On-Card Signals
6.2.3.10 Coagulation Waveform Control
EFI
The coag waveform generator consists of two S-bit shift registers, U226 and U227, wired together to form a 16-bit word. After receiving a start pulse to the ShiM...oad input (pin 15) from the randomizer control, U226 and U227 output pulses from pin 13 at a 0.5 J.lS rate (due to a 2 Mhz signal to the clock input) . The logic level of the output pulses is deter· mined by the fixed inputs (A through H) of U226 and U227. The final digital waveform is used by the RF Power Amplifier to form a damped coagulation waveshape . liming is as follows:
EF2
(a)
2.0 ' low;
(e)
(b) (e)
0.5 ' high; 1.5 ',low; 1.0 ' high;
(Q (g)
(d)
1.0', low; 1.0 ' high; 0.5 ',low.
U226 and U227 are locked out during the cutting mode since they are not required. 6.2.3.11
8 Mhz Shifter
The coagulation waveform requires that the base frequency of 1 Mhz be shifted approximatety ± 4%.
The base waveform is synthesized with a phaselocked-loop (PLL), U228, whose voltage controlled oscillator (VCO) output is approximately 8 Mhz. The 8 Mhz from the veo is divided down by U229 and fed back to one reference input of the PLL The second reference input is connected to a 62.5 Khz reference clock. The U229 divider has been designed to divide at a ratio that provides a near 62.5 Khz output.
ME N4
N5 N6 N7
RLYDLY TPA TPB
Low going signal from the randomizer controller, U225, to external flag 1 input on ~P Low going signal from A to 0 converter to external flag 2 mput on IlP Low going signal to ~p indicating selection of internal 64 byte RAM 1/0 select of DAC or ADC I/O select I/O select Output select of randomizer controller High going signal, after delay, to control high voltage relay High going signal from ~P indicating selection of high order memory address bytes High going signal from IlP indicating selection of low order memory address bytes
6.2.4 Sound Board 6.2.4.1 Digitalker
The Digitalker, U301, is started by a write pulse to U301, pin 4, from N3 and simultaneous data from the 8-bit data bus. Information written to the Digitalker determines which word is to be selected from the word list. The word list is stored in the EPROM , U203. Digital voice audio from U301 , pin 39, is buffered and filtered by U303. 6.2.4.2
Tone Generator
Tone generators consist of U305, U306, and U307. One tone, 390 Hz, is shared by both cut and coag modes. U30SC determines which of the two other tone oscillators are used. The tones are squelched whenever there is no footpedaJ activity or the Digitalker is accessed.
7
6.2.4.3
Volume Control
U309 and U310 are electronic volume control devices. The TONEVOL and TALKVOL signals detennine selection of either U309 (tone) or U310 (voice). The VOLUPoN signal determines the direction of volume: either up or down. The N3 signal strobes U309 and U310 for volume control function. The outputs of U309 and U31 0 are fed to U304 for final amplification to the speaker.
The oLY signal provides a small time delay upon power-up to quiet down the oigitalker and tone generators. U301, pin 6, generates an interrupt to extemal flag line 3, EF3, of the J.l.P when the oigitalker is active.
6.2.5 6.2.5.1
High Voltage Power Supply Board General
Relay K401 breaks both the AC and off-line DC voltages simultaneously for safety. A line voltage auto-switch mechanism is employed to select proper connection to either 1001120 or 220/240 VAC. Relay K400 has a 120 VAC coil connected across the primary of low voltage transformer, T701, so that when Tl01 is operated at 2201240 VAC, no AC voltage is presented to K400; and the d~ bridge, 08400, operates as a full wave bridge rectifier. When TI01 is operated at 100/120 VAC, K400 energizes and forces the diode bridge, 08400, and capacitors C401 and C402 to operate as a voltage doubler system. Relay K400 initially defaults to the 220/240 mode for safely. RT400 and RT401 provide inrush current limiting. R400 and R401 provide voltage balancing due to unequal leakage currents in C401 and C402. R402 provides a shorter discharge time for C401 and C402 when K401 is de-energized. Unloaded off-line voltage is approximately 330 VOC. High DC voltage monitoring is provided by optoisolator U400. Two separate DC grounding systems are maintained: isolated for off-line; and earth, for post-off-line and chassis. Unregulated high DC voltage is transferred from the off-line side (isolated) to the post-oft-line side (earth ground referenced) via FET 0400 and flyback transformer T400, 0400 is controlled by pulse width modulation (PWM) controller, U403, and pulses T400 by PWM at 125 Khz, During O4oo's off time, flyback energy is transferred from T 4OO's primary to T400's isolated secondary winding, R404, R405, C403, and C404 comprise two snubber circuits to prevent destructrve voltages from destroying 0400. Flyback energy is rectified by 0402 and filtered by C405, Regulated DC voltage is now available to the RF Power Amplifier. R449 and C440 provide snubber protection for 0402. Input to the PWM controller, U403, is derived from several sources, and combined before being input to U403, pin 9. The purpose of U403 is to maintain voltage regulation from several volts to as much as 225VDC.
8
oAC vottage (from the controller board) is first buffered by U404B, and then is applied to two locations: U404A and U401 B. 6.2.5.2
Voltage Sensing
U4018 compares DAC voltage and scaled down high DC voltage from C405. The ·reSultant output signal from U401 B, VCNTl, is applied to the data input on flip-flop U405A. VCNlL is combined with SYNC from the PWM controUer, U403, The output of flip-flop U40SA is lhen applied to U403, pin 9, the shutdown input. Scaled down high DC voltage that exceeds the DAC reference voltage causes shutdown of the PWM controller, U403. Synchronizing (SYNC) is used to preclude sporadic duty cycle pulses from occurring and causing premature shutdown of U403. 6.2.5,3
Current Sensing
DC pulse current through 0400 and T400 is isolated and monitored through current transformer, T 401 , and then applied to U401A. If peak current exceeds the reference set by the oAC voltage, the PWM controller, U403, is shutdown. Comparator U401A's trip point is modified by U404A At oAC reference voltages up to 3 VOC, U404A acts linearty; above 3 voe, U404A clamps. The purpose of this circuit is to prevent excessive high DC voHage overshoot during periods of light or no load while output DC voltages are less than 125 vec. With DAC voltages above 3 vec (greater than 125 vec at the output) ,the overshoot problem is minimal. Additional over-current protection is provided by U409. When current exceeds 10 amps at the output of the high vottage power supply, the PWM controller, U403, shuts down and a signal, SCMONI, is transmitted to the j.lP for error control handling (error code 02). The purpose of this additional circuit is to prevent destruction of the power supply and RF Amplifier. 6.2.5.4
lsolaled FET (0400) Drive
The PWM controller's clock provides an isolated bias voltage for FET driver, U402, Clock signal, SYNC, drives U406, Q404, and T403. T403 provides ~Iation between off-line and post-oft-line sides. The •A' drive signal from the output of U403 drives 0401 , T402, U402, and FET 0400. T402 also provides isolation. 6.2.5.5
Normal Operation (Flyback Mode)
The ftyback transformer, T400, operates in the discontinuous mode for light loads. That is, T400's primary current starts at zero, and secondary current drops to zero during each cycle. The flyback transformer operates in the continuous mode for heavier or transient load conditions, The continuous mode of operation is characterized by nonzero primary current at the start of each cycle, where the primary current immediately steps up, then ramps linearly (i.e., ramp on pedestal waveform).
62.5.6 ACIN_
On-Catd Signals 120/240 VAC input to diode bridge
DACOUT Buffered DAC output voltage PWM Pulse wktth modulated signal from PWM controller to power FET SYNC Buffered clock signal from PWM controller, U403 Signal from output of voltage sense comparator +15V/ISO Isolated 15 vott bias supply for power FET driver VCNTL
6.2,6 RF Power Amplifier Board 6 .2.6.1 RF Bridge Amplifier The RF Bridge Amplifier is of the 'H' bridge design. Each vertical hatf· leg of the 'H' is an FET suitably driven at 1 Mhz. The drive signals ate 01 Mhz and 0 1Mhz. (See description under Controller Board) . Each alternate half-leg (i.e., top left/bOttom right; bottom leftltop right) is driven in phase . Voltage is supplied from the coag waveform generator to the top haff-legs of the bridge amp ~op left; top right) , marked BRIDGE . The load, T501 , is placed as the horizontal bridge across the middle of the two vertical elements . 62.6.2
Coag Waveform Generator
DC voltage to power the RF Bridge Amplifier is controlkld by the coag waveform signal driving 0501 . When in the cut mode , 0501 is fully saturated and allows pass·through of the voltage from the High Voltage Power Supply. During the coag mode, the coag waveform signal (see description in Controller Board) modulates the voltage supplied by the High Voltage Power Supply . The modulated DC voltage is filtered by L501 , L502, L503, C508, and C509 into a decaying DC voltage waveform, thus forming the damped sinusoidal signal through the RF bridge amplifier. Cut-off of DC voltage to the RF bridge amplifier is provided by U503 and the PWRDIS signal under conditions of short and open circuit at the forceps. 6.2.6.3
RF Output Steering
The RF output transformer, T501 , is prevented from saturating by a DC blocking capacitor, C528, in series with the primary winding. T501 's secondary comprises two sepatate windings; one low impedance and one high impedance. Coag and low power cut modes ate very low impedance «20 ohms) ; high power cut is somewhat higher «300 ohms) . Switch. ing secondary windings is controlled by relays K501 , K502, and the CUmL Y signal. When required, the high power cut secondary winding is added in series with the coag/low power cut winding to achieve the desired higher impedance.
The high power cut winding added in series with the coa9'low power cut winding, instead of a tap-type connection. limits the amount of high voltage energy generated in the high power cut winding when the coagulation mode is used. This excessive noise energy can create interference problems both inside and outside the metal case of the CMC-1I1. Further coag noise filtering is pro*d by a low pass filter consisting 01 L505, L506, L507 , C531 , and C532 . The coag noise filter also provides proper matching between RF output transformer T501 . the forceps cord , and biologlcalloading at the forceps. Transformer TS02 and L504 , C529 and C530 are part of the Open Circuit Detector, and is explained in the Mother Board description. 62.6.4
Short Circuit Oetection
Two short circuit detection circuits are used; one each for coagllow power cut and high power cut. Current through the forceps is sensed by R525 for coagflow power cut, or RS24 for high power cut. The sense current , in the form of a small voltage, is rectified, filtered, and detected by opto-isolators U513 or U515 when the threshold is exceeded. The outputs of U513 or U515 cause the one-shot timers in U514 to operate at 100 millisecond (ms) intelVais as long as excessive short circuit current is present. The outputs of U514 are ORed together to form the signal PWRDIS . During the 100 ms period, voltage to the RF bridge amplifier is cut off. At the end of the 100 ms period, RF power is restored to test again for a shorted condition . This cycle continues until the short circuit is removed . The PWRDIS signal is also shared by the Open Circuit Detector. An LED marked 'short circuit' is used during testing to confirm operation. The purpose of short circuit detection is to prevent excessively high RF currents from destroying the RF Power Amplifier and forceps. 6.2.6.5
Isolated Bias Supplies
Isolated Bias Supplies of 7.5 VOC are required for the upper hatves of the RF bridge amplifier and the coag waveform generator. These stages 'float' with respect to earth ground when operating , and must have the Isolated Bias Supplies. 6.2.6.6
On-Card Signals
BRIDGE
ISO+7V(n)
ISOGND(n)
PWRDIS
Modulated DC vottage (during coag) from coag waveform generator fitter to RF bridge amplifier Isolated 7.5 vec bias power supplies to RF bridge amplifier and coag waveform generator Isolated grounds of bias power supplies to RF bridge amplifier and coag waveform generator Signal from output of short circuit detectors to disable RF output
9
SCRES1
SCRES2
SCRES3
SCRES4
Short circuit current through R525 to input of coagllow power cut short circuil detector Short circuit current through R525 to input 01 coag/low power cut short circuit detector Short circuit current through A524 to input of high power cut short circuit detector Short circuit current through A524 to input of high power cut short circuit detector
6.3 MASTER LIST OF CARD CONNEC· TOR SIGNALS AlDIN
o to 5 vec signal to the analog to
BUNK
digital converter (ACC) 1 Hz signal; 75% on, 25% off
Low going signal from 1/0 indicating selection of external irrigator
LPCUT
High going signal from 1/0 indicating selection 01 Jow power cut mode
LT
Low going signal to Display board indicating selection of LED test mode High going signal from ,...p indicating a memory read function
MRD MUTELED
High going signal from 1/0 indicating selection of mute LED
MUTESW
Low going signal to I/O indicating depression of the mute switch
MWR NOHV
High going signal from IlP indicating a memory write function Low going signal to 1/0 indicating unregulated htgh voltage DC is present on the High Voltage Power Supply (HVPS) board Output select for displays on display
COAG
High going signal from I/O indicating selection of roag mode
N1·N2
COAGFTSW
Low going signal to 1/0 indicating depression of coag footswitch
N3
Output select for Digitalker and volume controls; input select for I/O
COAGRST
Low going signal to 1/0 indicating depression of the coag reset switch
OCMONI
Low going signal to 1/0 indicating an open forceps condition
COAGSTAB
Low going signal to 1/0 indicating selection of coag power switch
PWMON
COAGWVFM
Digital signal to RF Power Amplifier (RFAMP) representing the coagula· tion waveform
CUOFTSW
Low going signal to I/O indicating depression of cut footswitch
CUTRST
Low going signal to I/O indicating depression of the cut reset switch
Q1MHZ
Low going signal to HVPS indicating selection of pulse width modulator (PWM) IC to stan output voltage supply to RFAMP Additional low going signal from output of open circuit detector to RF AMP to disable RF output Digital 1 Mhz signal with a 37% ·onduty cycle
CUTALY
Low going signal from 1/0 indicating seledion of high power cut winding of T501 via cut control relays
Q1MHZ
CUTSTAB
Low going signal to 1/0 indicating selection of cut power switch to 5 VOC signal from the digital to analog converter (DAC) to the HVPS Bidirectional 8-8it Data Bus Low going signal from Digitalker to external flag 3 input on f.1P
DAC DB[O .. 7] EF3 FTPDON
o
High going signal from I/O indicating depression of any footpedal
board
PWADIS
RFPWR1 RFPWR2
Same as Q1 MHZ, but 180' out of phase RF output power to patient output jacks RF output power to patient output jacks
SCMONI
Low going signal to I/O indicating an overcurrent condition on the HVPS
TALKVOL
Low going signal to volume controls on Sound board indicating selection of voice volume control
TONEDN
Low going signal to 1/0 indicating depression of the Tone Volume Down switch Low going signal to 1/0 indicating depression of the Tone Volume Up switch Low going signal to volume controls on Sound board indicating selection of tone volume control Signal to 1/0 indicating selection of cut or ceag power control; high for up and low for down
HPCUT
High going signal from 1/0 indicating selection of high power cut mode
HVRLY
Low going signal from 1/0 indicating selection of high voltage mains relay, located on the HVPS board
TONEUP
IRIGLED
High going signal from 1/0 indicating selection of irrigate LED
TONEVOL
IRIGSW
Low going signal to I/O indicating depression of the irrigation switch Digital signal from infrared receiver to f.1P
IRRECV 10
IRRIG
UP/DN
Low going signal to I/O indicating depression of the Voice Volume Down switch Low going signal to I/O indicating depression of the Voice Volume Up switch
Its purpose is to zero out the high voltage available to the RF Power Amplifier. Unregulated high voltage DC, however, remains on the High Voltage Power Supply board and must be approached with caution. Removing the ground turns off LED 201 and the unit announces 'output power is on'.
VOLUPDN
Digital signal to volume controls on Sound board representing volume direction
WATTS LED
High going signal from 110 indicating selection of watts LED Low going signal to I/O indicating depression of the Watts switch
6.4.4 Pin #4 Calibrate ON/OFF Grounding this pin enables the calibration function by announcing 'calibrate output power'. Refer to Section 6.6, Calibration, for details.
VOICEDN
VOICEUP
WATTSW 20KHZIN
20 Khz (approximate) sine wave from output of open circuit detector filter
20KHZOUT
20 Khz (approximate) sine wave 10 input of open circuit detector fiNer
+200V
0 to 225 VDC @ 2 Amps from HVPS to RF AMP
6.4 TEST POINTS Eleven test points are available to facilitate trouble shooting. All test pins are easily accessed al the top of the controller board on P203 (Figure 8). Activate test functions by grounding (momentarily or constantly, refer to each section for details) the appropriate pin. Note that some test points provide dual function capability.
6.4.1
Pin *1 Display Test/Power Up Momentarily grounding this pin provides a complete, sequential test of aU LEOs, lamps, and numeric LEOs. For Power Up, see 6.4.4, Calibrate On/Off.
6.4.5
Pin #5 Factory Profile This test point can be activated only when there is a problem with the EEPROM . This can occur during first time power-up with a blank EEPROM , or when the EEPROM malfunctions. When momentarily grounded, the unit announces 'recycle memory' and reprograms the EEPROM. Transferring data is seen in the coag display. When finished, the unit announces 'memory is correct' (assuming no EEPROM problems) and then reinitializes the CMC·III. With an error condition, the unit announces 'internal memory error' and flashes '01' in the microcut display.
6.4.6 Pin #6 RAM Read Grounding this test point causes an instantly calculated checksum of the EEPROM to be compared with the checksum stored within the EEPROM. The compared values show on the high power cut and coag displays. If the compared sums are equal, the unit announces 'internal memory is correct.' When this test point is ungrounded, the unit reinitializes. 6.4.7 Pin #7 Factory Test Grounding this test point causes the unit to announce 'internal power recycle on. ' This mode is available for factory use only. It is recommended that this test point NOT BE ACCESSED.
6.4.8
Pin #8 DAC Reference Voltmeter test point. OAC reference input voltage should be 4.75 VOC, ± .05 volts.
6.4.9 Pin #9 DAC Output Voltmeter test point. DAC output voltage. When in calibrate mode, this voltage can be compared against the displayed DAC value shown on the numeric LED display. The DAC output VOltage should be [DAC display/255} * (DAC reference voltage). Figure 6. Controller Board Layout
6.4.2
Pin #2 Sound Test/Power Down Momentarily grounding this point provides a complete. sequential test of all Digitalker words, tones, and voice/tone volume control1unctions. For Power Down, see Calibrate On/Off.
6.4.3 Pin *3 Deactivate PWM Grounding this point turns off the PWM controller IC on the High Voltage Power Supply. The message ·output power is off' announces and LED 201 turns on. This test mode allows full functioning of the CMC-III except for output power.
6.4.10 Pin #10 ACC Input Not used.
6.4.11 Pin #11 NOHV Bypass Grounding this test point allows operation of the CMC-lll with the High Voltage Power Supply board removed. It requires that the two High Voltage Power Supply board connectors, J403 and P404, be can· nected together to provide AC power to the low voltage power supply transformer, T70l. This test point must be ungrounded for normal operation with the High Voltage Power Supply connected.
11
Cut Output
6.5 OPERATIONAL PERFORMANCE The MALIS Bipolar Electrosurgical System CMC-III may be tested for operational performance using 50 ohm and 400 ohm noninductive test loads and AF ammeter or equivalent electrosurgical analyzer. A test set up in the accompanying figure shows typical values for each power setting. It should be noted that these are typical values and that output power may vary depending on line voltage, load resistor tolerances, and meier accuracy.
-- = '-(
O:a...
<
/ ~
/
powuM
-.
Typical Output vs. Power Setting
•
10 15 2< />
25 30 35 40 45 SO 60 70 60 90
100 110 120 130 140 lSO
12
0.7 1.0 1.. 3. 5. 7. 9. 11 . 14.
17. 19. 22
...
25. 29. 32. 35. 40. 45. SO.
Co.g. Output Into 50 ohms
0.12 .15 .1.
.. .,. ..'. .32
.53 .56 .62 66
..
0.71 0.76 0.60
0.' 0.89 0,95
1.00
100 110 120 130 140 lSO
0.7 1.0 1 .• 3 5 7 9 11 14 17 20 40 60 60 100 120 140 160 160 200
.12 .15 1. .24 .32
.,.
... .43
.53 .56
.22 .32 .39 .45 .SO .55 .59 .63
Output Powel (Watts)
0 .72 1.1
1.' 2.9 5.1 7.2 9.3 11.5
Into 50 Ohms
/
/
14.1 /
16.8 20.0 40.0 60.0 60.0 100.00
120.00 140.00
160.00
.67
180.00 /
.71
200.00
Into 400 Ohms
I
/
Anyone, or aU, of the CMC-IIJ's 40 power output settings may be calibrated individually by changing the target DAC calibration value (as stored in memory) associated with each setting. DAe value adjustments may be performed with the CMC-III in the calibration mode.
Figure 9. Tnt S.,t Up
Output Current (RF emp)
c'
Output Current (RFAmp)
6.6 CALIBRATION
RF Ammeter (0-1 8fl1)S)
Power Setting Mode (Melle Units) (Wens)
90
no n·i!Hluc!;v c re.<;!lor for hiSh.
60 70 60
/
U... 50ohm l00 waII non·j!ldocti'i: rerisIor fot oo.,g. and micro tut m 2.SO waa
(For reference only)
/
R;-
y
10 15 / 20 Micro- 25 30 C' 35 40 45 SO
0
0
,
)
0
/
CMC-I II
= =
Power Setting Mode (Mill. Units) (WItts)
output Power (Wett.)
0.72 1.1 1.. 2.9 5.1 7.2 9.3 11.5 14.1
16.8 19.2 21.3
23.3 25,2
28.9 32.0 353
39.' 45.1 SO.O
The calibration mode may be invoked by grounding pin 4 of P203 (refer to Section 6.4.4). With this pin grounded, the message ·calibrate output power' announces, and two numbers appear on the front panel numeric LED windows. One of the numbers is the Malis Unit setting of the previously selected mode; the other corresponds to the setting's target DAC calibration value. The DAC value may be increased by momentarily grounding pin 1 of P203, or decreased by momentarily grounding pin 2 of P203 (as a safety precaution, DAC settings may be changed by no more than ± 15 steps from the original factory supplied settings) .
The output power associated with a setting's new target DAC value may be confirmed by measuring the unit's output current as described in Section 6.5, Operational Perlormance. Note that the remote control is not functional during the calibration mode. Therefore, use the front panel rocker switches to change from one power output setting to the next, use the foot pedal to activate the output. If errors occur during calibration, or if the user wishes to restore the original factory set DAC targets, momentarily ground pin 5 of P203 to reload the standard DAC calibration values. When calibration is complete, remove the ground from pin 4. The unit announces 'calibration oW and then reinitializes at Malis Unit settings of 35 in both microcut and coagulate modes.
6.7 TECHNICAL SPECIFICATIONS Power Requirements 100 ±. 10% VAC with 100 selected on the supply voltage selector 120 ± 10% VAC with 120 selected on the supply voltage selector 220 ± 10% VAC with 220 selected on the supply voltage selector 240 ±. 10% VAC with 240 selected on the supply voltage selector SO/60Hz 400 Watts
Fuses External For 100 or 120 VAC operation: Two 4.0 Amp Type T (MOL) (125 VAC) For 220 or 240 VAC operation: Two 2.5 Amp Type T (MOL) (250 VAC) Internal Mother Board: Two (F600, F601) 3.0 Amp Type F (AGC) 250 VAG One (F602) 0.5 Amp Type F (AGC) 250 VAG High Voltage Power Supply Board: F400: 4.0 Amp Type T (MOL) 250 VAC for 100/120V operation 2.5 Amp Type T (MOL) 250 VAG for 220/240V operation F401: 2.0 Amp Type F (AGC) 250 VAG
F402: 1.0 Amp Type T (MOL) 250 VAG for 220/240V operation 0.6 Amp Type T (MOL) 250 VAG for 220/240V operation
AC Leakage Current Less than 10 ,.tA with power ON or OFF, polarity normal or reversed, with ground open or connected.
Output Waveforms Coagulate: Damped Aperiodic, centered at 1 MHz Cut: Sinusoidal, 1 MHz
Output Power Range Coagulate (20 settings) .72-50 watts into 50 ohm noninductive resistor load Micro Cut (10 settings) .72-16.8 watts into 50 ohm noninductive resistor load Cutting (10 settings) 20-200 watts into 400 ohm noninductive resistor load
Output Setting Indications Visual: Three-digit indicators, except micro cut, which is two-digit Aural: Voice annunciator (synthesizer)
Power Controls AC: ON/OFF Switch RF Output: Panel mounted three-position rocker types
Panel Connectors Bipolar: Two high voltage jacks
Cooling Convection; no fan
Weight 21 lb. (10.4kg)
Dimensions 8'/2H x 12 3/.W x 17D inches 21.6H x 32.4W x 43.2D centimeters
Minimum Operating Temperature 50'F (10'C)
Remote Control Power Source Two 1.5v AAA alkaline batteries
13
6.8 TROUBLE SHOOTING GUIDE
1.
2.
Unit does not operate (Power-on indicator light)
Low power output
a, Blown fuse
a. Replace fuse
b. Loose wire at power cord plug
c. No power at wall outlet
b. Check plug for wiring c. Check electrical service
a. Low line voltage
a. Adjust to 120, 220, or 240
b.lncorrect test load
c. lntemal calibration change
3.
Erratic power output
Correction
Probable Cause
Symptoms
volts nominal, as appropriate b. Use 50 ohm nonir.ductive load for coag and microcut; 400 ohm for regular cut c. Return for service and recalibration
b.lntermittent break in forceps cord
a. Gently clean plug surfaces with abrasive cloth b. Replace forceps cord
a. Loose or dirty connections
between forceps cord and jacks 4.
No power output
a . Broken wire in forceps cord
a. Replace forceps cord
5.
Excessive leakage current
a,Shorted output transformer
a. Check for shorting to core case. Retum for service and recalibration
6.
Excessive power output
a.lntemal calibration change
a. Retum for service and recalibration
7.
Voice indicator announces 'Internal fuse'. Power Setting Display flashes '00'
a. Blown internal fuse
a. Replace internal fuse
B.
Voice indicator announces 'Memory error'
0. . Operating
0. .
9.
Voice indicator announces 'Error'
a. Two front panel setting controls pressed simultaneously
a. Use care when pressing controls
10. Voice indicator announces 'Footpedal error'
a. Two footpedals pressed simultaneously
a . Use care when depressing footpedal
11. Voice indicator announces
a. Operating malfunction
a. Return for service
malfunction
Return for service
'Internal power error'
7.0 REPLACING INTERNAL FUSES Significant changes in the supply voltage setting, such as from 11 0/120V to 220/240V, require a change in two internal fuses. Fuses F400 and F402 are located on the power supply board. Figure 10 shows the location of the power supply board in the CMC-Ill chassis. 1. Disconnect the generator from the power supply. 2. Remove the six Phillips head screws and washers holding the cover in place. Remove the cover. 3. Remove the Phillips head screw (Item A in Figure 10) that holds the power supply board to the metal bracket. 14
A
Figure 10. Power Supply Board
4. Firmly pull the power supply board upward until rt can be disengaged from the card holders on either side. Do not attempt to pull the board completely out of the chassis; it is still connected via the supply voltage wiring. 5. Remove fuses F400 and F402 (see Figure 11); replace with appropriate type and value fuses (see Section 6.7, Technical Specifications).
G 8
Cleaner (J&J Medical catalog no. 3415). If tips become pitted or misaligned, retum the forceps to Codman Repair Service for repair or replacement.
8.2 Bipolar Cord low or erratic performance may be due to poor contact between the bipolar forceps cord plugs and isolated bipolar output j3cks on the generator. Badly oxidized surfaces impede current flow. Use an abrasive cloth to gently clean plug surfaces. Inspect the bipolar cord before each use; replace it upon evi· dence of deterioration. NOTE: Pulling plugs from the jacks of the MAUS CMC·1I1 by grasping the cord may damage the cords and cause intermittent operation. Disconnect the plugs by holding the plug with one hand and the generator with the other.
8.3 Pneumatic Footpedal .,Ct..'
l-SA.!
u:o...
A! lDCVINV'::
AT U' ..... ~ ' ..::
A; loell2W'::
UA'Ar~~'
F'9ure 11 . Changing Intemal Fuses on Power Supply Board
6. Slide the board back into the card holders, ensuring the pins on the bottom of the board align with their connectors. Push the board down firmly until the pins seat property in the connectors. 7. Replace the screw holding the board to the bracket Replace the cover and six screws and washers. WARNING: The supply power setting drum, located on the power receptacle at the rear of the generator, must also be set to the correct voltage and property fused for the electrical outlet before turning on the generator.
8.0 MAINTENANCE
Storing the pneumatic footpedal with the pneumatic tubing tightly wrapped around it may damage the tubing. leave sufficient slack to prevent stress on the tubing. Inspect the tubing before each use and replace the footpedal upon evidence of deterioration.
8.4 Electric Footswitch Storing the electric footswitch with the footswttch rord tightly wrapped around it may result in damage to the cord. Leave sufficient slack to prevent stress on the
com.
NOTE: DO NOT IMMERSE the footswitch in liquIds during use. The pedals should operate freely with a positive mechanical action. Inspect the footswitch cord before use for deterioration. Do not operate if the vinyl cover is damaged. The vinyl covered footswitch is not a repairable item. Replace the footswitch assembly as supplied by the manufacturer.
8.1 Bipolar Forceps
8.5 Power Cord
Proper care and maintenance of the bipolar forceps is essential to efficient cutting and coagulation. Dr. Malis states the following:
Never use extension cords, three-prong to two-prong power plug adaptors, or extra length power cords with the MALIS CMC-IJI. Before each use, visually inspect the power cord and plug for frayed or broken insulation. If necessary, replace the power cord with the same type, length, gauge, and insulation.
·While some sticking and charring of the bipolar cutting and coagulation forceps is unavoidable, the elimination of the initial overvoltage spike in the MAUS CMC-III waveform greatly reduces the incidence of sticking and charring. Coupled with additional waveform modifications, the MALIS CMC-1I1 can be used with less irrigation (or no irrigation at all, if required) while reducing sticking and charring to levels lower than heavily-irrigated spark gap and solid state generators. Because the generator is effective at lower settings, pitting of the forceps tips which normally occurs is greatly reduced.· Remove coagulum deposits as often as necessary to keep working surfaces clean. This ensures the flow of current between forceps tips. We recommend Johnson & Johnson Medical's Electro-Surgicaf Tip
8.6 Remote Control The remote control uses two 1 .5v AA. alkaline batteries. To open the battery compartment, press down on the lower portion of the remote's rear cover and slide it down. Remove the old batteries. Insert new batteries as illustrated within the compartment. Slide cover back on until it snaps into position.
15
9.0 ROUTINE CLEANING The MAUS CMC-III generator cabinet may be cleaned with a damp doth or sponge. Use alcohol or mild c~aning solutions to remove stains or adhesives that stick to the cabinet. DO NOT immerse the MAUS CMC-III generator or remote control in any liquid. Subjecting the generator to excessive mois· ture may damage the electronic components and violate the warranty. The CMC-III lootpedal may be w-'d with normally used hospital cleaning liquids. Do not aJlow liquid to enter the white plastic footpedal connector.
10.0 STERILIZATION Never steriliZe the MALIS CMG-Itl generator, pneu-
matic tootpedaJ, electric footswitch, remote control, or connecting cable. Place the remote into a sterile plastic bag similar to those supplied for operating
room cameras. The Integrated Irrigation Tubing and Cord Set is a single-use device, sold sterile. Do not resterilize.
11.0 BLOCK DIAGRAMS
16